The MedCAD AccuPlate devices can reduce time in the operating room.
DALLAS — This article was originally published by our content partners at the Dallas Business Journal. You can read the original article here.
Dallas-based MedCAD, a medical technology company, is seeing success with new 3D-printed surgical devices that can expedite recovery for patients.
MedCAD has unveiled 3D-printed titanium implants referred to as AccuPlate 3DTi — customizable plates used by surgeons in facial reconstructive surgeries. While MedCAD has been making titanium implants for years, the new 3D-printing technology dramatically accelerates the speed of production.
When patients are facing surgery due to trauma, tumors, orthodontic work, or other oral/maxillofacial surgery, doctors take a scan of the area and send it to MedCAD. Its engineers and designers then work to create a titanium plate for that specific patient that will provide surgeons with guidelines for optimal recovery. Not only do the implants save time in the operating room, but they also remove mechanical stress caused by manual plate bending.

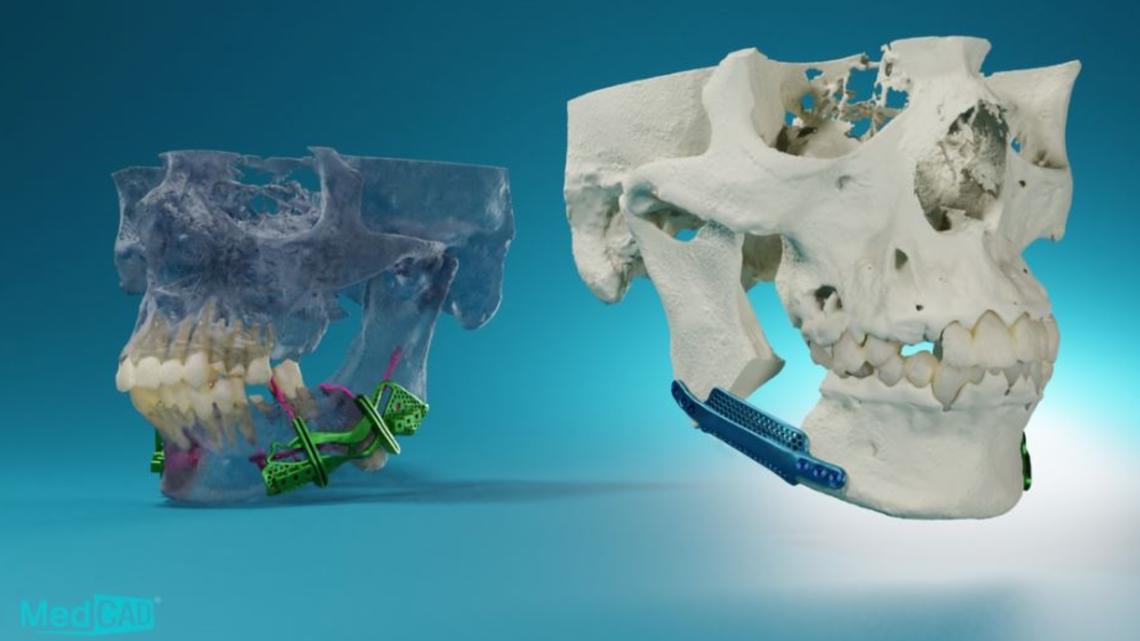
It’s a process that MedCAD CEO Nancy Hairston said has transformed reconstructive surgeries. Prior to the 3D printing technology, it would take nearly a week to mill each individual implant out of titanium. Now, implants are created six to a tray, and can be printed overnight with more customizable features.
The plates are delivered to doctors in as few as five days after surgeon approval.
“We’re solving problems that haven’t been solved,” Hairston said.
Hairston founded MedCAD in 2007 after working as an artist, designing toys for Mattel and Disney. Today, MedCAD employs more than 50 people and is growing.
Surgeons took MedCAD’s 3D-printed facial implants to Ukraine earlier this year to operate on soldiers injured in battle. Doctors reconstructed the faces of soldiers who lost their eyes or were shot in the face, all using the AccuPlate 3DTi technology.
MedCAD, which operates legally as Vanduzen Inc., partners with distributors to ship its products nationwide and to South America. It has a manufacturing facility in Plano and an office in Deep Ellum that can now 3D-print the titanium implants — a notable addition to the health care ecosystem in the neighborhood next to downtown, which is also home to a 22,000-square-foot manufacturing facility for Mark Cuban Cost Plus Drugs.